Product overview
Magnetron sputtering forms an orthogonal electromagnetic field above the surface of the cathode target. When the secondary electrons generated by sputtering are accelerated into high-energy electrons in the falling region of the cathode, they do not fly directly to the cathode but in the orthogonal electromagnetic field. Under the action, the high-energy electrons continuously collide with gas molecules and transfer energy to the latter, making them ionize and turning themselves into low-energy electrons, eliminating the bombardment of high-energy electrons on the substrate.
Technical parameter
Device model |
VLT-1000 |
VLT-1200 |
VLT-1300 |
Coating room size |
Φ1000×1250 |
Φ1200×1250 |
Φ1300×1500 |
Ultimate vacuum |
10-4Pa |
10-4Pa |
10-4Pa |
Pump down time |
No-load normal temperature pumping to 5×10-3Pa<10min |
Film thickness meter |
Configure vibration thickness gauge |
Evaporation source |
Resistance evaporation |
Student target |
One pair (intermediate frequency) |
Cylindrical target |
One |
High pressure bombardment |
3000V 600MA |
3000V 600MA |
3000V 300MA |
Workpiece bias |
1000V 20A 500 40A |
1000V 20A 500 40A |
1000V 30A 500 60A |
Workpiece rotation method |
Single/6/8 revolution revolution planetary gear structure |
Configure the unit |
K-600、ZJP300 |
K-600、ZJP300 |
K-800、ZJ600 |
2X-70 |
2X-70 |
2X-70 |
Inflation system |
Gas mass flow controller |
Baking temperature |
350℃ |
Control system configuration |
Automatic control PLC and touch screen |
Note: The configuration with * is returned by the user, and other specifications can be customized by the user
Equipment principle diagram
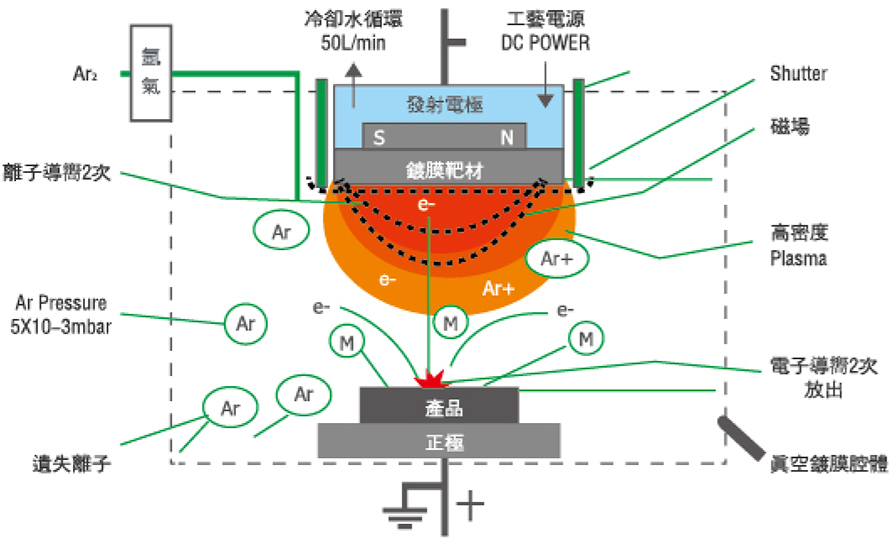
Schematic diagram of magnetron sputtering coating
When a certain amount of gas (such as argon) is charged in a suitable vacuum environment and a 60 kilowatt DC power supply is used, a high voltage of several hundred volts will be generated to generate an arc. In the arc environment, ions and electrons conflict with the target to produce coating Effect.
Equipment characteristics
Production period: The production period is short—60sec/1 the same period (conditions for dry products without a large amount of gas release)
Coating material: suitable for various metal coatings (aluminum, nickel, copper, chromium... and other metal materials)
Coating method: metal sputtering coating and protective coating are completed continuously (no other anti-gasification treatment is required after coating)
Coating quality: high brightness, strong adhesion, good finish products can be directly coated without primer coating after injection
Coating speed: two 60KW high-power magnetron sputtering electrodes, instant and large-scale coating
Dehumidification capacity: The vacuum chamber is equipped with a low-temperature refrigeration system below minus 140 degrees to fully absorb moisture to increase the vacuum reach speed
Operating expenses: The sputtering electrode is a self-developed product, which greatly improves the use efficiency of the target material
Defective product rate: omit the usual processing procedures (primer coating and aluminum film protective paint spraying) to reduce defective products
Occupied area: loading and unloading at a fixed position requires only a small operating space
Operation method: The man-machine interface can be set and monitored intuitively, and the person who has no management password can not change it
After-sales service: There is an after-sales service center and parts warehouse, which can quickly deal with problems in use
Magnetron cathode
Equipped with optimized magnetron cathode between poles. For ordinary reflective coating applications, the equipment will be equipped with intermediate frequency stations for working cleaning, plasma enhanced chemical vapor deposition bottom protective coating, high-rate sputtering evaporation coating, plasma enhanced chemical vapor deposition surface protective coating and other corresponding films Layer craft room.
Fully automatic process control and integration
The hardware and software design of the equipment can be organically combined with the conveyor belt of the customer's production line. The conveyor belt is responsible for transferring the workpiece rack to the loading station of the equipment, thereby transferring the workpiece to the coating station of the equipment. When the workpiece enters the unloading station, the conveyor belt receives the workpiece rack and transfers the workpiece to the next production position. The equipment passes and The precise coordination of the conveyor belt helps customers further improve production efficiency, reduce production costs and increase productivity.
Satisfy customers' high production requirements
The control system including the man-machine dialogue interface can provide fault diagnosis, alarm function and data log management. The installation positions of the various components of the equipment, such as cathodes, driving devices, and valves, fully take into account the needs of maintenance and repair work. The design, material selection and manufacturing of the model fully reflect the Vilit vacuum equipment guidelines.